By, Jackie Wei Green, Senior Communications Leader, Arup, Los Angeles
Arup is proud to be working with the tech firm WoHo to make off-site construction more affordable, greener and easier to scale. Founded by a group of engineers, designers and architects with ties to Massachusetts Institute of Technology and Georgia Tech and based in Cambridge, Massachusetts, WoHo is seeking to build out manufacturing operations and advance pilot projects in the US.
Arup’s integrated multidisciplinary team of experts is providing consulting in SMEP engineering (structural, mechanical, electrical and public health) and for building code and Americans with Disabilities Act compliance. A pilot project is slated to kick off in Boston in 2021, which will put the WoHo team one step closer to achieving its goal of revolutionizing the way prefabricated buildings are designed and constructed.
WoHo aims to create a single, streamlined platform that supports the design, manufacture and construction of high-quality buildings with unprecedented precision and efficiency. The WoHo system uses a series of discrete foundational components that can be scaled and configured to span residential and commercial buildings such as multifamily housing, hotels, dormitories, labs and offices. The design and engineering behind the components can be reused, driving efficiency and consistency and enabling a high level of customization available to each project.
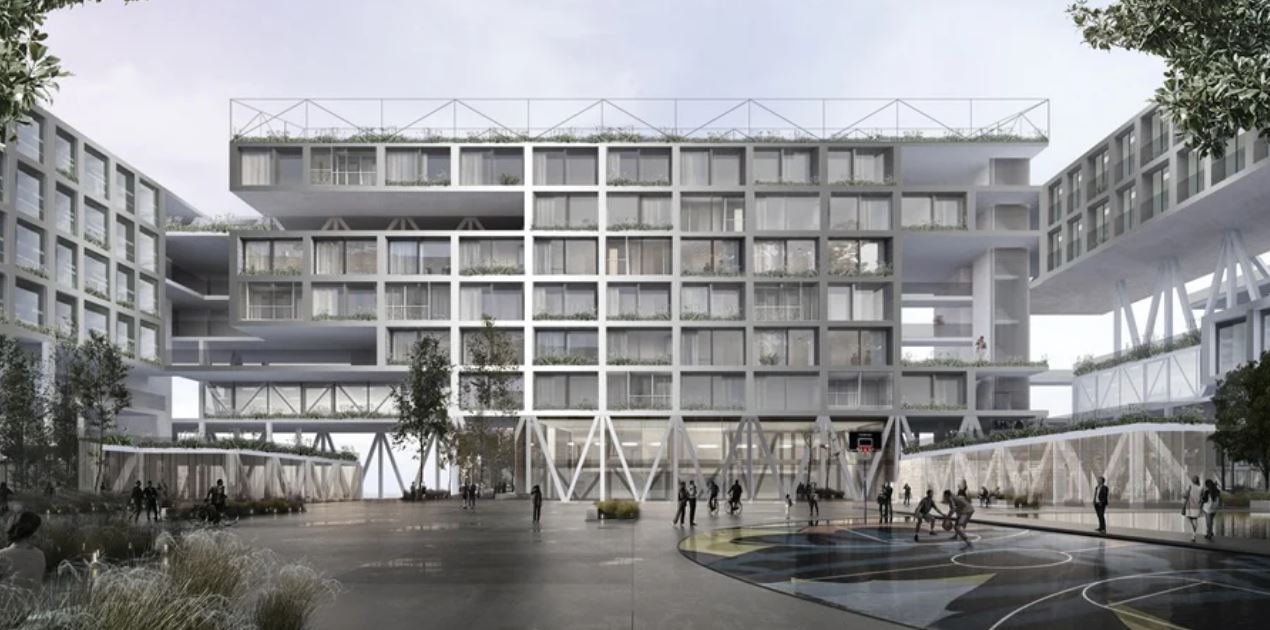
“While modular construction has existed for decades, it has suffered from an association with low-end, low-quality materials,” WoHo CEO and cofounder Israel Ruiz said in a statement. “[WoHo] will disrupt home and multi-use buildings, as developers and suppliers can more quickly and efficiently meet sustainability standards to address affordability and the housing shortage.”
The ultimate objective is to radically improve construction time, affordability and sustainability of high-quality buildings. Commercial and residential developers will be able to design and construct more economical, longer-lasting buildings without having to sacrifice architectural style or jeopardize carbon emissions targets.
“At WoHo we are front-loading the building design and engineering process for architectural and environmental benefit. We are bringing the insight and knowledge of respected experts to collaborate with our in-house team assessing our products and crafting a successful path from factory to market,” said President and cofounder Debora Mesa.
WoHo has enlisted the help of Arup’s off-site construction experts to achieve this breakthrough. Arup has earned a reputation for designing technically-robust modular solutions in the US. One such project is 19-story Citizen M Bowery in Manhattan, New York. Most recently, Arup has developed a report analyzing the high-rise modular construction industry, commissioned by the Canadian Standards Association (CSA Group).
“Arup is committed to sustainable development and we are proud to collaborate with clients like WoHo who are aiming to provide housing which both is affordable and has a low carbon footprint. By making prefabricated construction more economical, sustainable and scalable, the WoHo system could help urban planners and developers address some of the most pressing challenges faced by today’s cities,” said Arup Principal and project director Mark Walsh-Cooke.
About ARCHEN News
ARCHEN news is a digital media platform for the AEC | MEP | HVAC community.
Interesting project? Send for consideration.
contact@archennews.com or (646) 494-5102